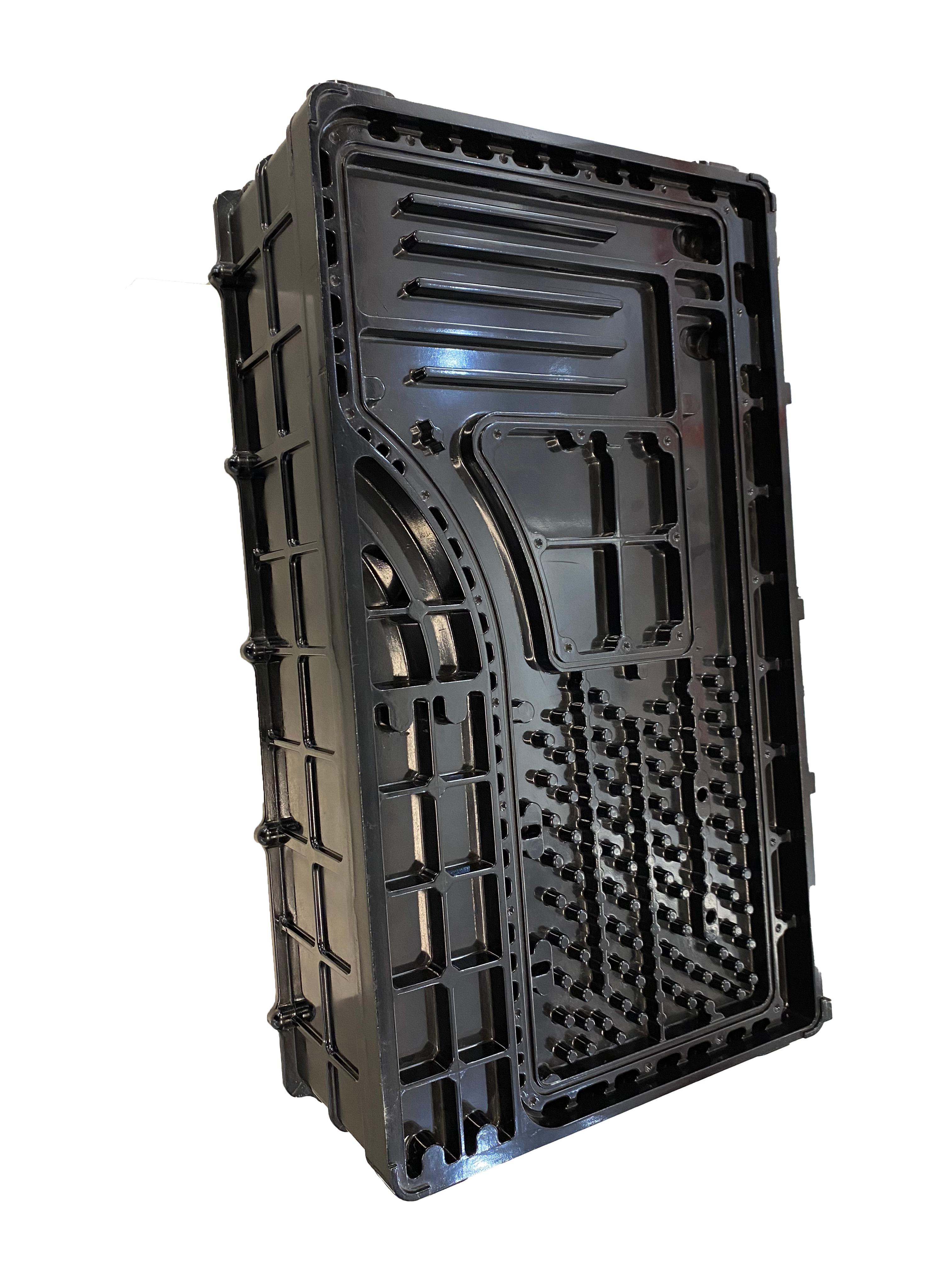
Release agents have the following common features:
- No staining mold, the surface of the casting product is white and bright, showing the unique characteristics of aluminum metal. It has a strong demoulding effect and eliminates the trouble of sticking to the mold.
- The emulsion has strong thermal stability, can withstand higher typing temperature, does not emit smoke, and does not carbonize. Very low volatility reduces smoke generation.
- With low surface tension, the release agent can effectively wet the entire surface of the mold, including its fine mold.
- The cooling speed is fast and the spraying time is short.
- The emulsion has the stability of storage, dilution, freezing and thawing.
- Good anti-mucosal ability and emulsion protection, prolong the life of the mold.
- Clear physical properties, in line with environmental protection requirements, can be certified by third-party sgsrphs.
It is very important that the release agent does not contaminate the mold. "Popier Bocko" release agents are thermally stable. It does not crack when the temperature is raised, while other mold release agents can "burn" to produce carbide deposits that contaminate molds and products. The surface of the product is black or black, and the size of the mucus film or product is often inaccurate. The product qualification rate is low.
Basic requirements for release agent quality
- The effect of release agent and good demoulding effect can save maintenance and replacement of injector pins and sliders.
- The surface of the casting is bright, the surface defects of the parts are easier to find, and the long-term storage can prevent mildew.
- There are many reasons for porosity in castings due to less porosity. If the release agent is not resistant to high temperature and insufficient adhesion, "gasified" release agent will be produced in the aluminum material, forming pores at the moment of aluminum flushing.
- Low surface tension (ie the release agent has no sticky feel). When the worker sprays water, even if the water spray is not good, the mold release agent can penetrate the entire surface of the mold to complete the mold release. The technical requirements for employee water spray are not high, avoiding the possibility of new employees making mucous membranes or waste.
- The release agent is thin on the mold surface, as low as 0.2 microns, can withstand the impact of aluminum water, and can quickly cool the mold, saving spraying time and the molding cycle. Due to the different thicknesses of the mold, the production error of each machine is about 10% per day.
- No carbon deposits in the mold. Carbon deposits are carbon and high temperature lubricants left over when the release agent "burns". In severe cases, a 0.1-0.3 mm thick film is formed on the mold surface, which affects the heat transfer of the mold and leads to prolonged part formation period or frequent mold burning. If the parts are removed by cleaning and saving the mold, it will affect the efficiency and life of the mold.
- Less smoke, no black smoke. Otherwise, the steel structure of the workshop will be polluted or rusted, and the health of employees will be damaged, especially in winter.
- The composition of the release agent should be non-corrosive and non-toxic. Otherwise, the steam produced by the water spray will be more or less sucked into the employees and adsorbed on their skin, causing the employees to contract diseases such as pneumonia or rashes.
- Emulsifier Emulsifier has the stability of storage dilution, freezing and thawing, which reduces storage conditions and saves electricity.
- Requirements with clear material properties and compliance with environmental protection requirements can be verified by a third party.
- The recyclability of the release agent, so as not to discharge to the outside, such as the use of cutting fluid, not only saves the cost, but also avoids the possibility of polluting the river.
- The quality of subsequent processes such as electroplating, anodizing, spraying, and dusting mustn't be affected. This is the last process before the product is shipped, and the cost of scrap is high.
Conclusion
For more information about ejector pins in die casting, the world's largest die casting machine, and die casting machine tonnage calculation, we are glad to answer for you.